Spray-applied Fire Resistive Material (SFRM) are proprietary mix of natural thermal insulative mineral (Vermiculite or Perlite ) with a cementitious bonding medium ( Gypsum or Portland cement.
Application of SFRM can be a tricky undertaking. Many owners, construction managers and even contractors don’t realize what they’ve gotten themselves into until it’s too late. Since spray contractors already have the equipment to apply, they are often assumed to be competent and up to the task. However, these teams may not have a strong knowledge of fireproofing technics, material , standards and end up failing to apply the material properly, resulting in misses, under or over applied product, curing issues and schedule problems.
Many times it is too late and the material has so many issues that it must be removed and the process has to start all over. Other times the issues aren’t as bad, but still lead to significant project delays. With a little help from an experienced consultant, you can avoid these schedule and budget busting issues in the first place.
So what are the areas to be taken care off and how one can avoid falling into the trap?
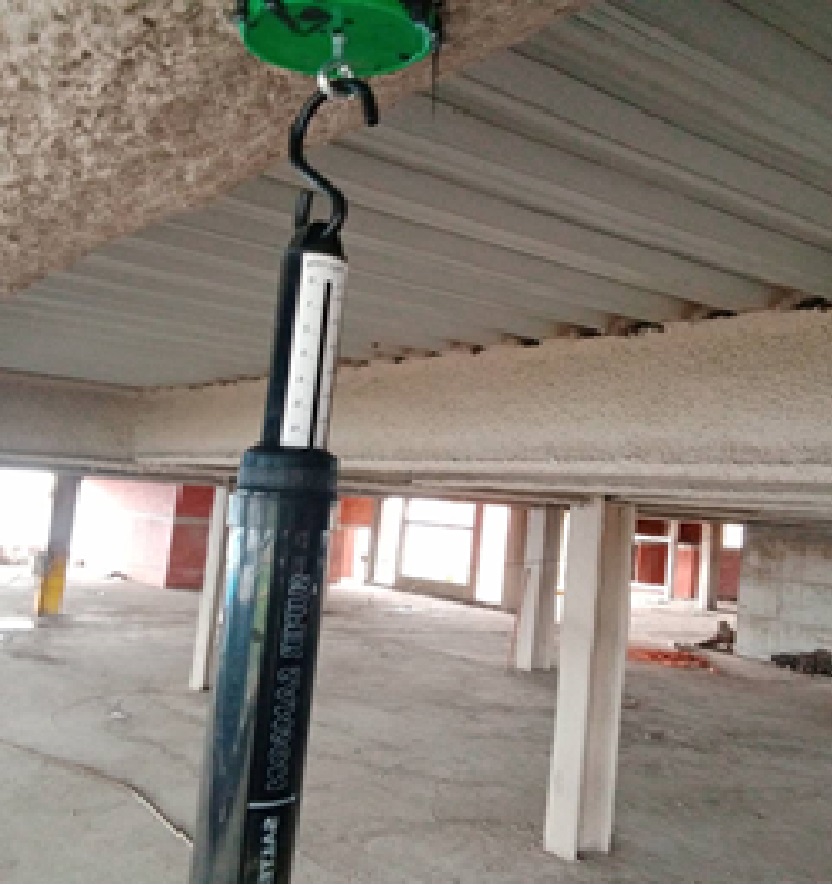
Bond strength check before application
Steel members are normally painted with protective coating. The protective coating may be various types of primers or even PU coat. The bonding between protective coating and SFRM during fire and also during the life are key to success of fireproofing. SFRM datasheet never specify any protective paint, but bonding strength or adhesion strength varies.
Where surface is already primed, the details of the primer should be collected and discussed with SFRM supplier. Alternate method is to apply a mockup coat and having bond strength checked up. Thumb rule for bond strength pass value is 80% of value in product data sheet.
In case of non achievement, the SFRM supplier must be contacted for a tie coat or other action to be taken.
Substrate surface Quality
Steel surface may have mill scale rust, Oil, Grease, flaking material, dried cement slurry, dried mud which can affect SFRM bonding with the surface. While, mud, heavy dust , grease, oil can be removed easily, rust and cement slurry shall be difficult for cleaning. The existing rust shall be increasing under SFRM in later date, due moisture hold in it. However cumbersome, the rust patch should be required for removal by chemical or grinding method. Reapplication of primer may be made for protection.
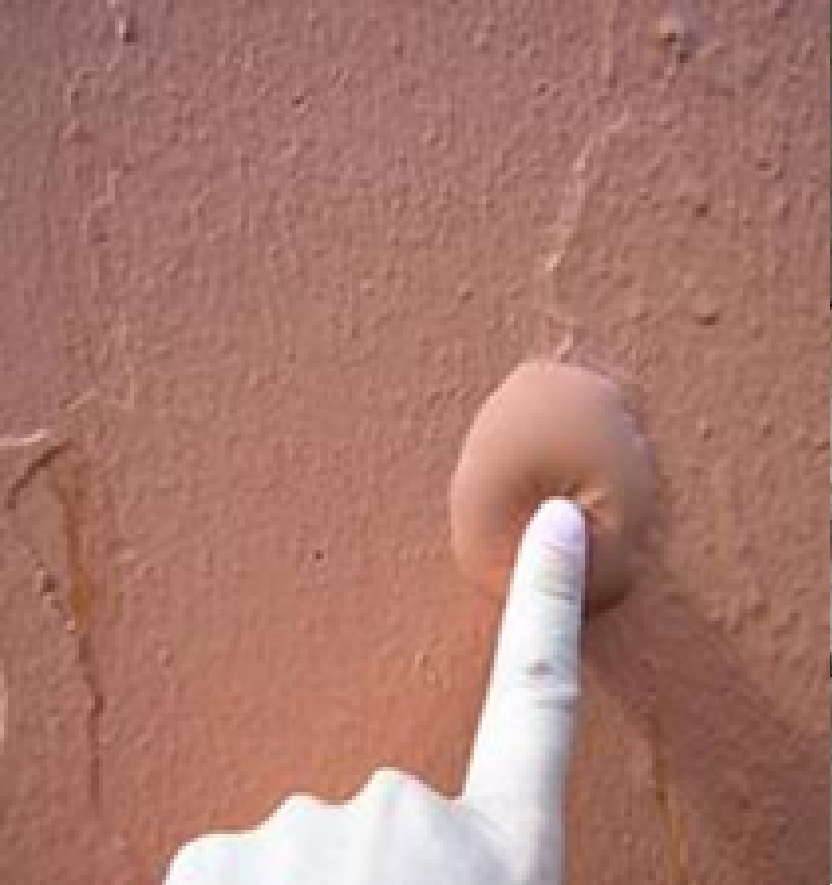
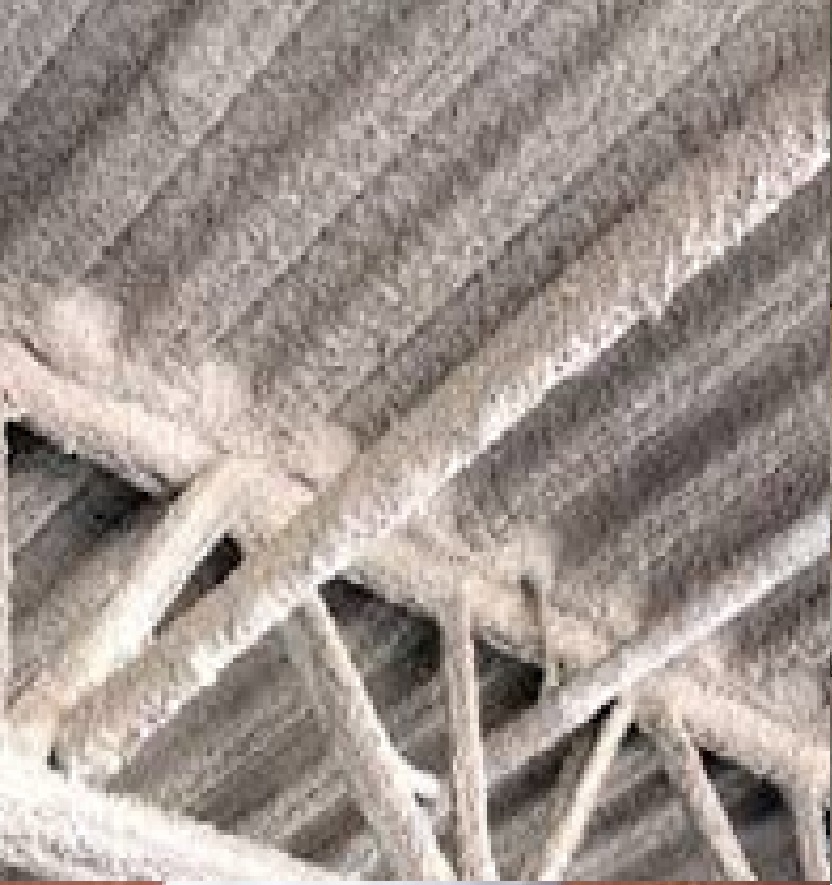
Failure to take environmental condition in to account.
SFRM fireproofing needs to be applied within a set temperature and humidity range. A quick drying of sprayed SFRM, shall not allow curing process. Quick drying of surface also leads to generation of cracks which leads to the application pitfall…. Hence depending upon the environmental condition, mixing of water with SFRM or curing process by sprinkling extra water are regulated.
Judging of reinforcement need for SFRM spray.
Reinforcement requirement is decided based upon following .
- Specified in the design system.
- Specified in the Product datasheet.
- Advised by Material supplier or method statement.
- Thickness of coating is high and SFRM density is considerable
- The bending and torsional stress on fireproofing members where fireproofing carried in parallel with PEB floor construction.
Lack of reinforcement leads to development of crack within a year. Some time the sprayed material comes out like a plate.
The reinforcement quality depends upon mesh width, mesh fixing depth, mesh quality, pinning quality etc.

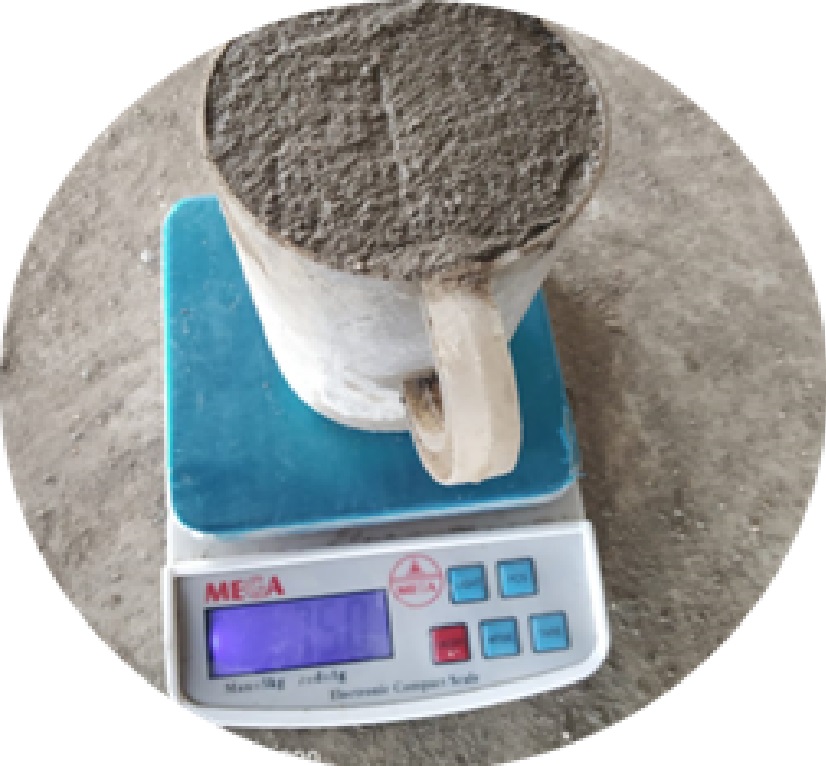
Control of SFRM mix ratio
Water and fireproofing material are advised to be mixed in a ratio ;say (Water X lit : 1 bag). X in liter is a range, which shall be decided based on humidity and temperature. If the surface of sprayed material dries up in 24 hours, more water should be added.
On contrary more water means, more over spray, more spray return etc.
However, a decision can be made for amount of water to be mixed and sprinkling of water for curing.
Usage time for mixed slurry & deciding minimum/ maximum thickness/ coat.
Delay in spray of mixed material, deteriorate the bonding quality of sprayed material. PDS or material supplier shall always be consulted on maximum time for use of mixed slurry.
Maximum thickness to be sprayed per coat is also advised by PDS. Minimum thickness of spray is assumed to be 6 mm, as it may lead to quick dry up resulting lowering of cohesive strength with previous coat. The applicator needs to set control limit and find methods to achieve.
Example : Thickness of SFRM as per design : 18 mm. Maximum spray / coat 12-15 mm as per PDS. The applicator may achieve 18 mm by applying ist coat of 10 mm and 2nd coat of 8 mm.
Judging recoat time
In multiple coat application, any subsequent coat must be applied before the previous coat is dry. This makes both coat to cure as a monolithic coat over substrate. As a thumb rule, next coat should applied within 24 hours provided surface of previous coat is not fully dry. In such a case, the surface of previous coat is made wet by sprinkling water before recoat. However, no recoat should be carried after the surface is fully dry as both coat remains as two different layer and in presence of fire, top layer may spall.
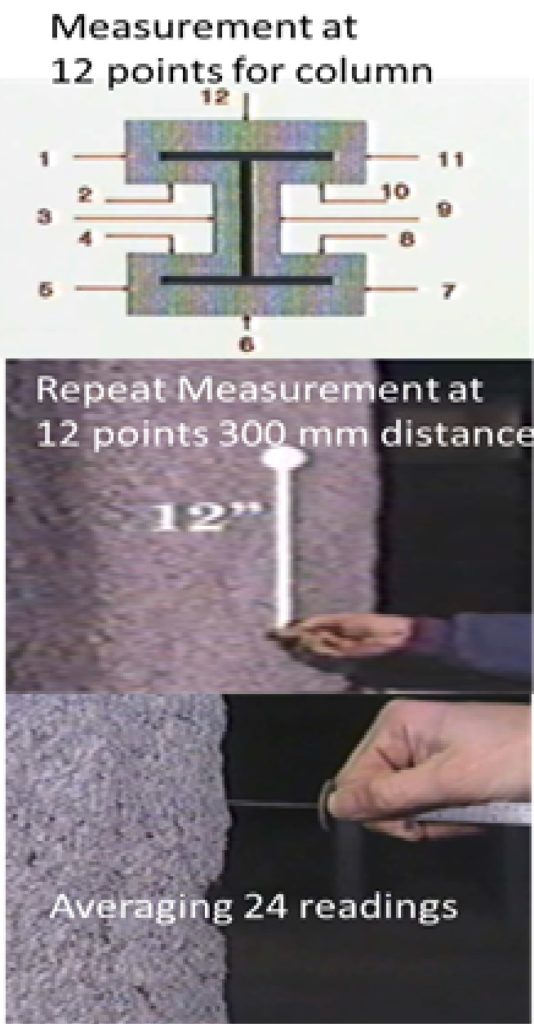
Ensuring Coating thickness uniformity.
Thickness of coating measured as per international standard. UL design defines thickness tolerances to be withing 25%. ASTM E 605 defines various points around steel members where reading are to be taken. These points also includes thickness measurement at edges of flange. The average of all reading must be more than the design thickness as per ASTM E 605. While depositing at edges are tricky but essential to avoid non conformity. Depositing additional layer at edges on later date shall not be permanent deposition. Special methods and training are required for successful deposition at edges.
The other extreme of spray application is over coating which shall consume higher material.
Additional fire proofing areas beyond steel supporting members.
Secondary members are not considered in fireproofing design but are to be sprayed as same thickness of joining primary members to avoid conduction of heat to primary members in case of fire.
Some time gaps exists between deck sheet and beams. In case of fire, temperature on beams shall increase due to conduction of heat. Hence these gaps are to be sealed with insulations and coated with SFRM.
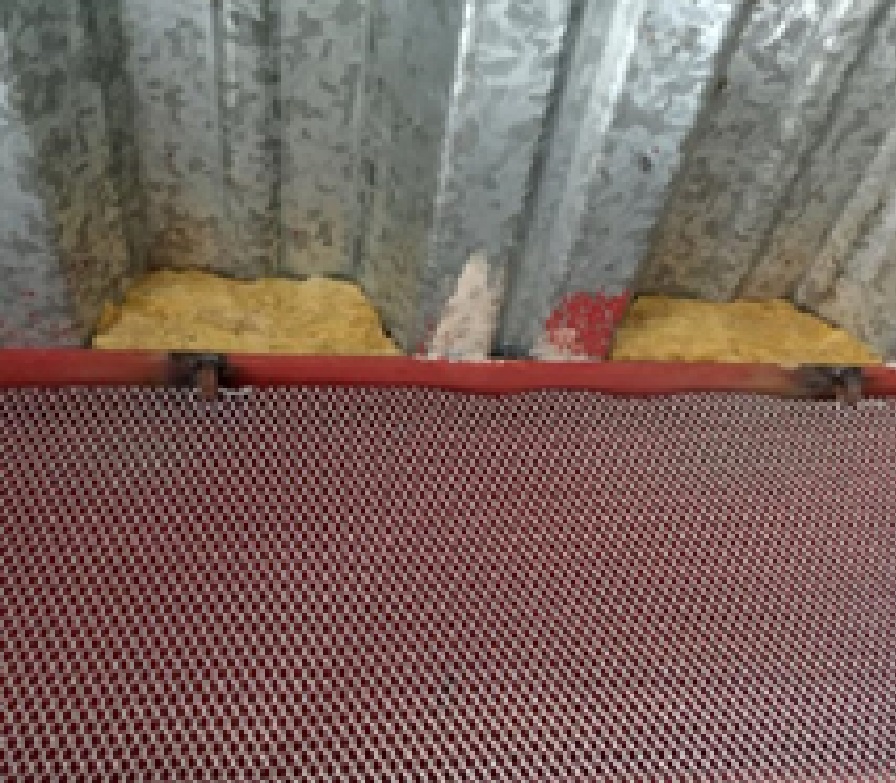
Repairing Technique
Cracks appears not only for deviation in following prescribed process but also due to external factors and factors beyond the control of applicators. Some time for testing and inspections, Fireproofing material are scooped out. For hanging HVAC ducts or fire hydrant pipes, fireproofing material are taken out.
The repairing procedure are defined by material supplier. The idea is to have proper bonding at the joint between new SFRM material inserted and old material on the surface.
Summery
While some key points are discussed for ensuring an effective fireproofing application, but the discussion is not exhaustive. It is advised that the applicator and its key persons are trained under supervision of the material manufacturer or the process of application is supervised by a trained inspector or a consultant.